View previous topic :: View next topic |
Author |
Message |
mrmike
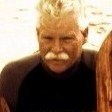
Joined: 06 Sep 2007 Posts: Location: coronado, ca
|
Posted: Fri Jul 23, 2010 10:16 pm Post subject: |
|
|
ply does not plane well the only planing that I do on ply is the rails and only by hand then block and sand the nose so the bottom is flat flat flat and real fast!!! _________________ PAIPO ON
blog http://mrmikespaipos.blogspot.com |
|
Back to top |
|
 |
gdog101
Joined: 20 Jul 2010 Posts: Location: Naples FL
|
Posted: Sat Jul 24, 2010 8:11 am Post subject: |
|
|
what is block and sand? lol This is the first time i have ever really worked with wood... _________________ green soul |
|
Back to top |
|
 |
mrmike
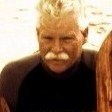
Joined: 06 Sep 2007 Posts: Location: coronado, ca
|
Posted: Sat Jul 24, 2010 9:16 am Post subject: |
|
|
I glue a block of hard wood on the top of the nose then shape it with a body grinder then sand it to shape
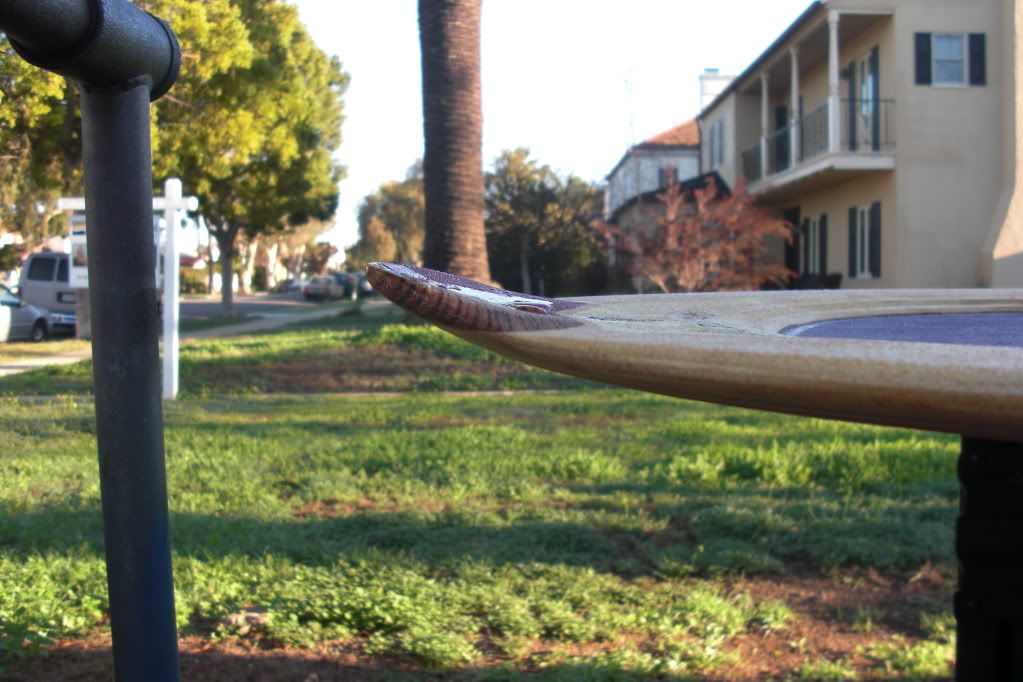 _________________ PAIPO ON
blog http://mrmikespaipos.blogspot.com |
|
Back to top |
|
 |
gdog101
Joined: 20 Jul 2010 Posts: Location: Naples FL
|
Posted: Sat Jul 24, 2010 4:26 pm Post subject: |
|
|
Sounds really hard
What do you think is best for glueing boards together? _________________ green soul |
|
Back to top |
|
 |
mrmike
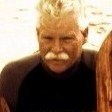
Joined: 06 Sep 2007 Posts: Location: coronado, ca
|
Posted: Sat Jul 24, 2010 5:39 pm Post subject: |
|
|
no so hard you have to start somewere. I use Titebond II wood glue get it at the home depot  _________________ PAIPO ON
blog http://mrmikespaipos.blogspot.com |
|
Back to top |
|
 |
gdog101
Joined: 20 Jul 2010 Posts: Location: Naples FL
|
Posted: Sun Jul 25, 2010 8:23 pm Post subject: |
|
|
is 11" to narrow? _________________ green soul |
|
Back to top |
|
 |
mrmike
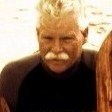
Joined: 06 Sep 2007 Posts: Location: coronado, ca
|
Posted: Mon Jul 26, 2010 9:32 am Post subject: |
|
|
11" might be on the narrow side. most of my longer boards are 14" to 16" wide and 48" to 60" long. but I have 2 that are 12" wide at the nose and 5" wide at the tail and the other way around, they work good but takes some getting use to. you can surf almost anything if you work at it
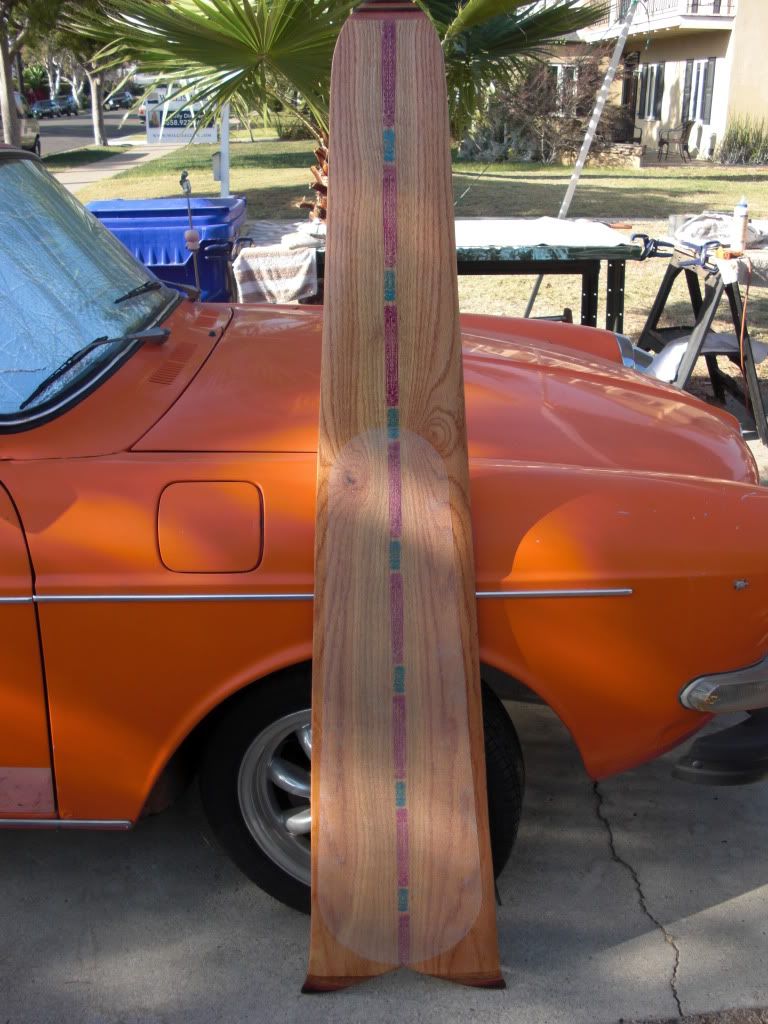 _________________ PAIPO ON
blog http://mrmikespaipos.blogspot.com |
|
Back to top |
|
 |
geoffreylevens
Joined: 18 Nov 2009 Posts:
|
Posted: Mon Jul 26, 2010 11:31 am Post subject: |
|
|
Mike, you use Titebond 2 rather than Titebond 3? Or was that just a miss-key? |
|
Back to top |
|
 |
mrmike
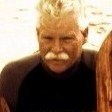
Joined: 06 Sep 2007 Posts: Location: coronado, ca
|
Posted: Mon Jul 26, 2010 1:22 pm Post subject: |
|
|
3 set to fast for me. if you want to tinker around with it use 2 If you are just going to glue two boards togather and clamp it you can use 3. both are the same except the set time and cost I think 3 cost a little more _________________ PAIPO ON
blog http://mrmikespaipos.blogspot.com |
|
Back to top |
|
 |
geoffreylevens
Joined: 18 Nov 2009 Posts:
|
Posted: Mon Jul 26, 2010 1:45 pm Post subject: |
|
|
Ahh, from reading their lit, I had the impression that 2 was maybe more water proof... Guess not though, you'd probably know as much as they do about that  |
|
Back to top |
|
 |
Uncle Grumpy
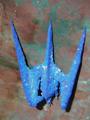
Joined: 15 Jan 2007 Posts: Location: San Clemente
|
Posted: Mon Jul 26, 2010 2:09 pm Post subject: |
|
|
IMO Epoxy is better then either. It was created as a marine adhesive. I like T88.
Titebond joints are a bitch to repair because it won't stick to itself.
These notes are from a very reliable source.
They are in reference to boatbuilding but of course a surfboard is just a tiny boat.
General Boatbuilding Notes on Glues and Goos
Resorcinol: The marine standard. If you can get 70 degrees F or higher for an overnight cure and consistent and high clamping pressure with no gaps, you won’t go wrong using it. Likes wood at 10-15% EMC, according to Navy tests. Long open time. Repairable with epoxy. Ugly red glue line.
Marine Epoxy: The repair and restoration standard. Bonds well to a wide variety of materials, and usable in almost all flexibility and temperature conditions. Needs no clamping pressure, only contact…fills gaps well. Likes wood below 12% EMC. Repairable with itself, joints can often be broken apart for repair with using heat. Clear glue line and can be dyed to match the wood. Controllable open time with different hardeners. Slightly permeable to water vapor and there are reports of failures in fully saturated wood and with White Oak. Very sensitive to UV, requiring protection.
3M 5200: A rubbery, polyurethane sealant in various colors with adhesive properties sometimes used as a glue. Fails as a glue under water saturation without high clamping pressure, and without the proper strength testing I couldn’t do here, it’s not recommended as a stand-alone marine glue. Repairable with epoxy.
Liquid Polyurethane: Gorilla Glue, Elmer’s Probond, Elmer’s Ultimate, and others. Versatile in temperature and bonding wet wood with moderate open time, these glues aren’t rated for below waterline use but initial use shows potential as a marine glue. Likes high clamping pressure and fits similar to resorcinol…it won’t fill gaps. Will successfully glue green wood at 30% EMC, although above 19%, anecdotal evidence suggests the wetter the wood, the weaker the bond. Repairable with epoxy. Noticeable, yellow-brown glue lines.
PL Premium Construction Adhesive: This polyurethane goo shows promise as a marine glue with further testing and use. Works like 3M 5200 but cures and behaves like liquid poly. Appears to bond well to everything epoxy does, and more where epoxy and liquid poly won’t, perhaps because of a higher isocyanate content…it bonds to difficult surfaces only cyanoacrylate super glues will bond to. The only general-use glue I’ve found that will bond difficult aliphatic-contaminated surfaces. Appears flexible to temperature and moisture content with gap-filling ability, but as a construction adhesive, its open time is shorter than liquid poly. Appeared to like high clamping pressure, and unlike other glues, wouldn’t bond at all without at least some. Repairable with itself and epoxy. Glue line as in liquid poly.
Urea Formaldehyde Plastic Resin Glue: Weldwood, DAP and others. The old interior furniture standard, and in older marine applications that required well-blended glue lines. Still preferred by many, as it is a no-creep glue easily repaired using epoxy. Long open time, it needs tight fits and 65 degrees F or higher for an overnight cure…it doesn’t fill gaps. Best glue line among them all and moderate water resistance still make it useful for interior marine brightwork applications. A relatively brittle glue and UV sensitive, it requires protection….but its brittleness is an aid to repairability, as joints can be broken apart for repair. An inexpensive powder with a short, one-year shelf life.
The Titebond Family of Aliphatics: Convenient. No mixing, just squeeze. Short open times, fast tack, and short clamping times. Fast, and an acceptable long-grain layup glue…in heated, commercial shops, I’ve had rough-cut Titebond panel layups in and out of the clamps and thru the planer inside of an hour. Flexible in temperature and to a lesser extent in moisture content, but the bottled glue can freeze in unheated shops. A flexible glue, it has been reported to creep under load, sometimes several years after the joint was made. The latest “Titebond III” appears to be a stronger glue than its two predecessors. Difficult glues to repair, as they won’t stick to themselves and no other glues will except cyanoacrylates, which are too brittle for general use. Epoxy and fabric aren’t bonding to aliphatic glue lines in marine strip construction, compounding repair difficulties. While not definitive, the new PL Premium appears to bond well to Titebond III residue and is worth pursuing by those repairing old white and yellow aliphatic joints. _________________ Prone to ride. |
|
Back to top |
|
 |
mrmike
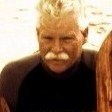
Joined: 06 Sep 2007 Posts: Location: coronado, ca
|
|
Back to top |
|
 |
|